Even a small glue smudge, a misaligned logo, or inconsistent paint finish can ruin a luxury brand’s in-store experience. For visual merchandising (VM) displays, precision isn’t optional — it’s everything. From acrylic glorifiers to metal risers, managing multi-material QA is key to consistent brand execution.
Table of Contents
At Samtop, we work with premium brands to build field-tested, defect-prevention systems across materials, finishes, and joinery — ensuring that every unit, in every region, performs visually as approved.
✅ Quick Summary for Featured Snippet
To prevent common visual merchandising display defects, implement QA controls like logo placement templates, glue masking, paint gloss checks, flame-polished edges, and CNC joinery tolerances. Use visual checklists, jig tools, and factory-facing instructions to catch flaws before they ship.
🧠 Why Small Visual Defects = Big Brand Damage
A 2mm offset logo or a bit of cloudy glue might seem minor at the factory — but for your flagship store or duty-free counter, it can undermine perceived value instantly. That’s why visual QA needs to move beyond tolerance tables and into real-world presentation control.
Ready to reduce post-install complaints? See how we support QA for global VM displays
🪞 Logo Misalignment
Problem:
Logo plate is off-center, angled, or uneven in pressure.
Causes:
No template, hand placement, tolerance drift in cutting.
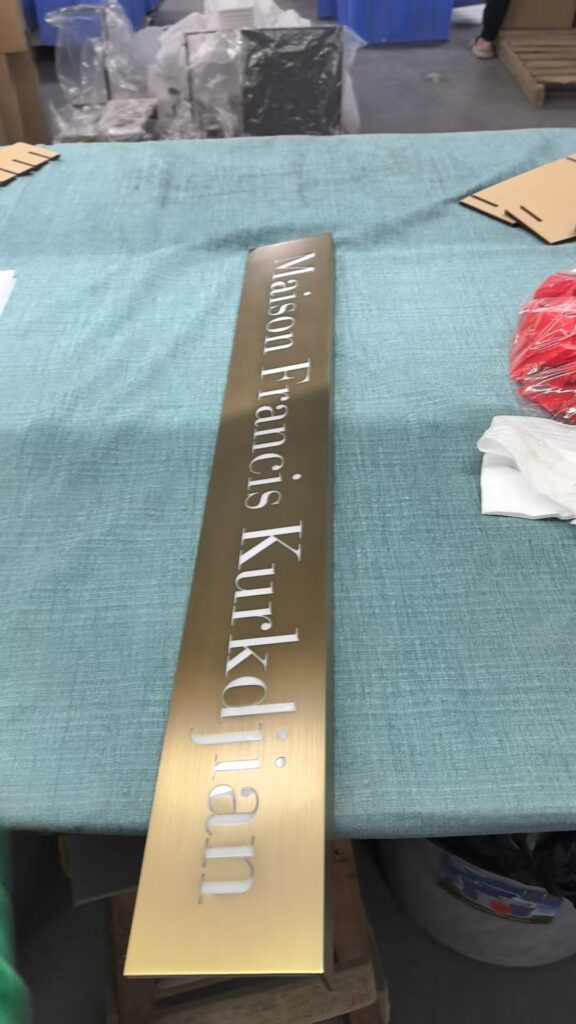
Solutions:
- Use laser-engraved jigs or stencil for logo placement
- Mark “logo zone” on protective film
- Approve logo print with digital overlay
- Add QC photo proof in your supplier’s QA workflow
📏 Tolerance standard: ±1mm
🧴 Visible Glue Residue
Problem:
Streaks, yellowing, or excess glue visible on clear acrylic.
Causes:
Wrong glue viscosity, rushed application, no masking.
Solutions:
- Solvent glue for acrylic = invisible bonding
- Tape masking on all visible edges
- Operator glue training with needle applicator
- Add UV inspection before film removal
📌 Reject units with any glue in lens zone or lightbox area.
🎨 Paint Inconsistency
Problem:
Gloss, color, or texture varies unit to unit.
Causes:
Poor mixing, no swatch control, spray distance fluctuation.
Solutions:
- Define gloss (e.g., 20% gloss on RAL 7035)
- Approve swatch + test 10-unit batch under lightbox
- Document master finish in display finish spec pack
📌 Gloss deviation > ±5% = fail for front-facing panels.
✂️ Edge Roughness
Problem:
Acrylic micro-chips, MDF fuzz, sharp metal burrs.
Causes:
Tool wear, no post-processing, rush routing.
Solutions:
- Flame polish acrylic
- Sand and seal MDF edges
- Deburr all exposed metal
- Include “edge safety” in your QA sheet with photo examples
✅ Luxury = smooth touch. No exceptions.
🔩 Misaligned Joinery
Problem:
Drawers stick, panels don’t flush, visible screw misalignment.
Causes:
Loose tolerance, swelling, uneven torque.
Solutions:
- CNC tolerance: ±0.3mm for visible joins
- Add dry-fit test before packing
- Label joints with assembly codes (A1–G1)
- Use locating pins or dowels
📌 Clean joinery is what separates premium from DIY.
💬 FAQ
Q: Can back-facing flaws be accepted?
✅ Sometimes — but define “non-visible” zones in your QA sheet.
Q: How do I ensure consistency across factories?
✅ Provide a visual checklist with images of correct and wrong examples.
Q: Is pre-shipment inspection necessary for all orders?
✅ For premium VM: always. Spot-check at least 10–15% with photo log.
✅ Conclusion: VM Quality Is Visual, Not Just Structural
- Don’t rely on “factory feel” — use jigs, gloss meters, ruler proofs
- Build QA around brand perception, not just specs
- Pre-approve with lightbox, angle check, and clean-fit trial
- Create a multilingual QA kit vendors can actually follow
- Track defects using a visual reject gallery
At Samtop, we turn your VM quality goals into measurable execution — so what’s approved is exactly what arrives.
📩 Want QA Tools That Speak Your Brand’s Language?
We offer:
🧾 VM-specific QA checklists
📐 Material + tolerance spec tables
📸 Defect gallery with red-flag image guide
🛠️ Bilingual inspection documents (EN + CN) for factories