There are many tests that can be done on the product or packaging before the retail display leaves the factory, all with the aim of ensuring that the customer receives a perfect product. The types of testing are as follows.
Table of Contents
1. Drop test
A large proportion of bespoke retail displays are made from acrylic bonded or wood assemblies, and if they are customized from another country, long-distance transport makes it easier to damage the products in the packaging. We test the goods before they leave the factory to ensure that the packaging is safe enough.
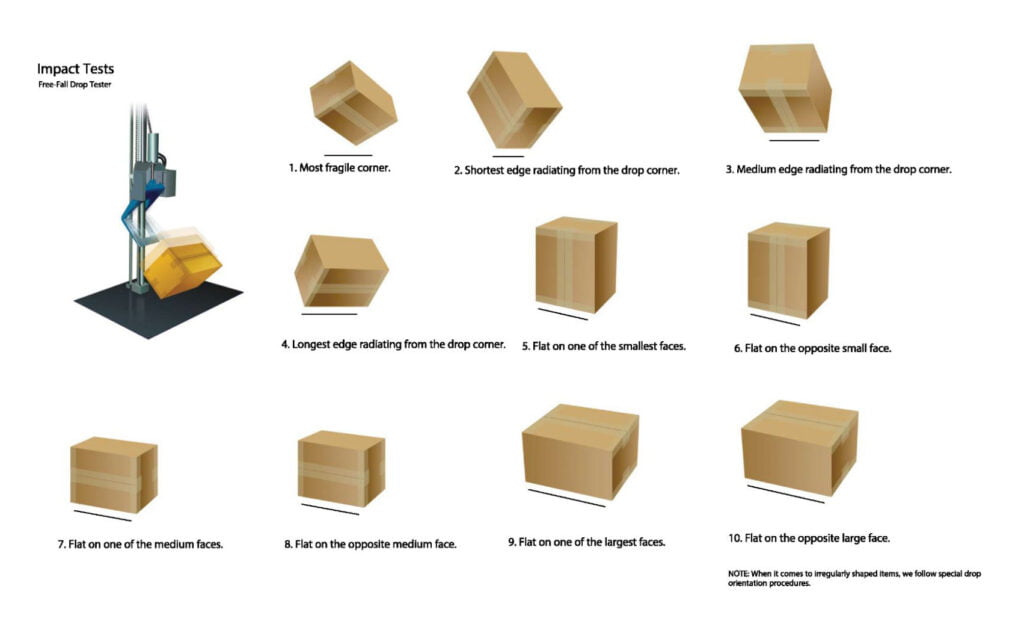
The package drop test is a type of test that is typically used to assess whether a product’s packaging properly protects the product during transport. After being dropped from a specified height, the package is observed for damage to the product inside after the impact.
Drop testing can be performed using a variety of methods, including drop towers, pendulum testers, and free-fall drop testers. The height and angle of the drop can be varied to simulate different types of impact scenarios.
2. Salt spray test
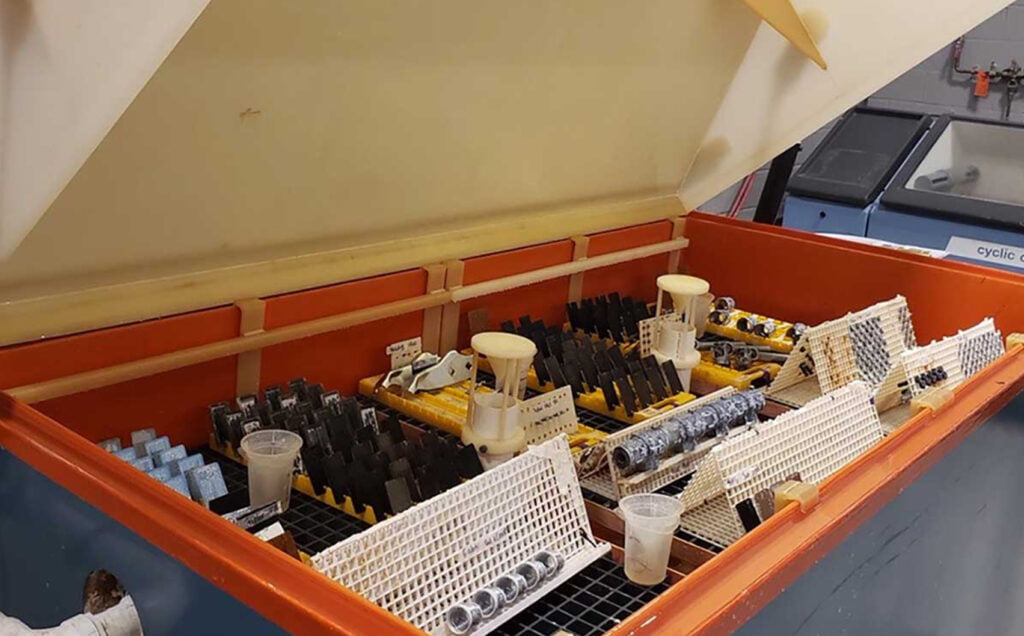
Retail displays are subject to corrosion on metal parts in a humid environment and wood parts may swell and deform, greatly reducing their service life, at which point we can arrange a salt spray test to measure the corrosion resistance of retail furniture finishes.
During the test, samples are exposed to a saltwater mist generated by a spray nozzle. The temperature and humidity levels in the test chamber are controlled to create a stable environment. The length of the test may vary but usually varies from a few hours to a few weeks.
Once the test is complete, the sample is inspected for signs of corrosion such as rusting, pitting, or discoloration. The extent and severity of the corrosion are then assessed to determine the resistance of the material to saltwater exposure.
3. Temperature test
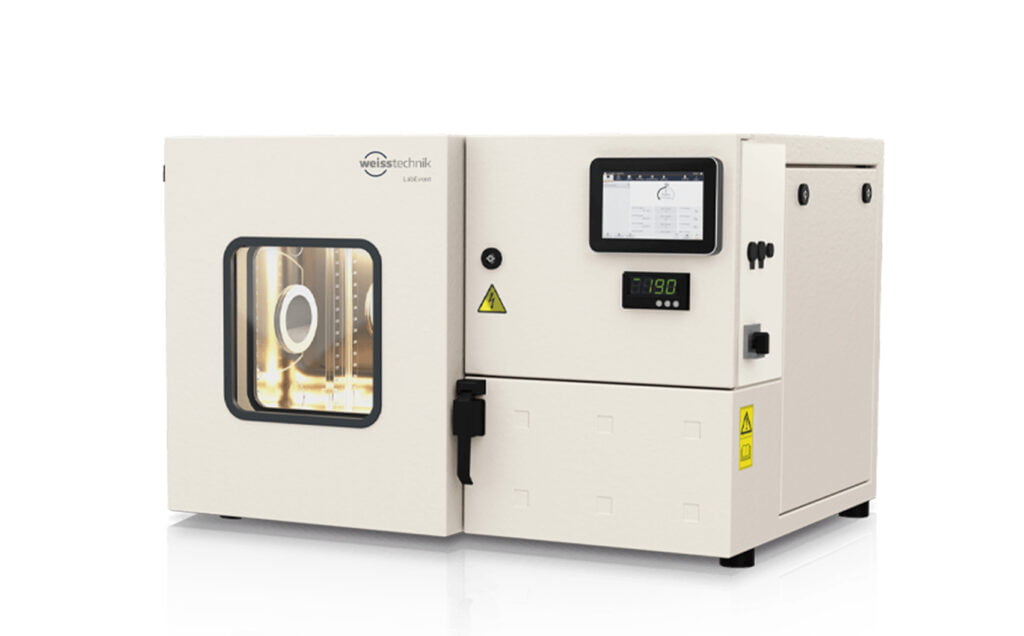
Temperature testing is a very necessary test before retail displays leave the factory. Temperatures vary across the globe, and some materials appear to expand and contract thermally after being shipped to cooler temperatures after being finished at higher temperatures, ink cracking on advertisements, and glass products being held up by items that expand and contract less thermally than it does.
Temperature testing assesses the performance and reliability of products and materials under different temperature conditions. By exposing retail displays to a range of temperatures for a period of time before they leave the factory and then observing their behavior and performance, potential design flaws are identified and the reliability of retail displays is improved. The results of temperature testing can also be used to improve the selection of materials and optimize manufacturing processes.
4. UV resistance test
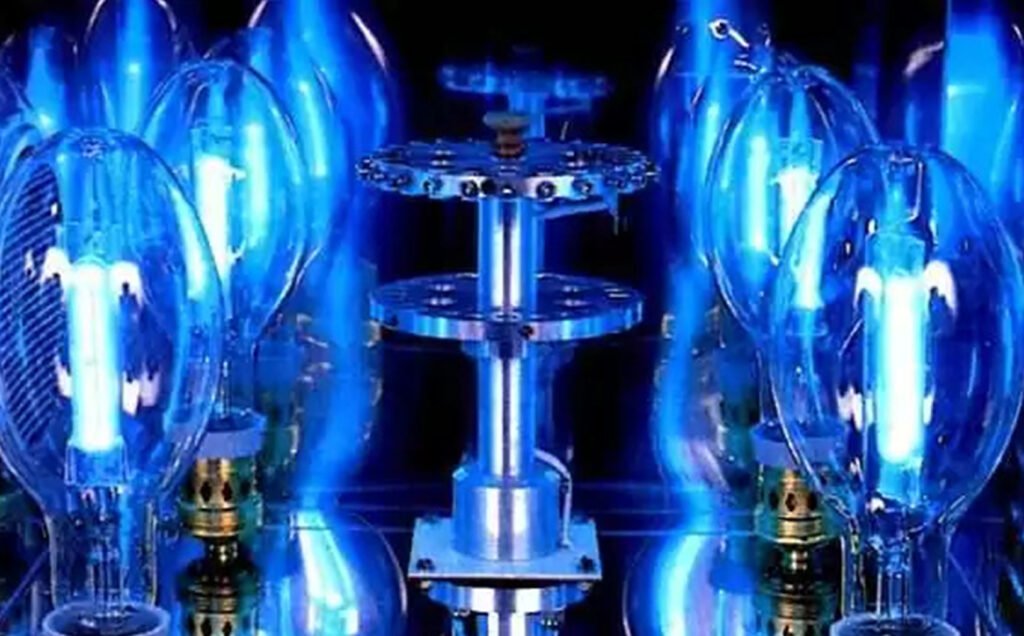
UV resistance testing is commonly used in industries such as textiles, plastics, coatings, and outdoor equipment. Outdoor advertising and shop windows on street-level storefronts are exposed to sunlight for a significant amount of time and if the materials used to manufacture retail displays are UV-exposed and are prone to fading and cracking, this can add significantly to the cost of the display.
The test usually exposes the retail display to UV radiation for a period of time and then evaluates its performance against various criteria. Large sculptures made from foam, inks used in canvas advertising, and plastic panels are all materials that are susceptible to UV deterioration and it is best to use materials that have passed the UV test.
5. Alcohol test
We are not talking about the alcohol test carried out on drivers here, but rather testing whether the inks on the merchandise information and advertising images on retail displays are susceptible to chemicals such as alcohol, especially as displays selling goods containing alcohol such as perfume should use inks that are difficult to melt off by them. Alcohol should be used to swab screen printing inks and coloured inks at the proofing stage.
6. Scratch testing
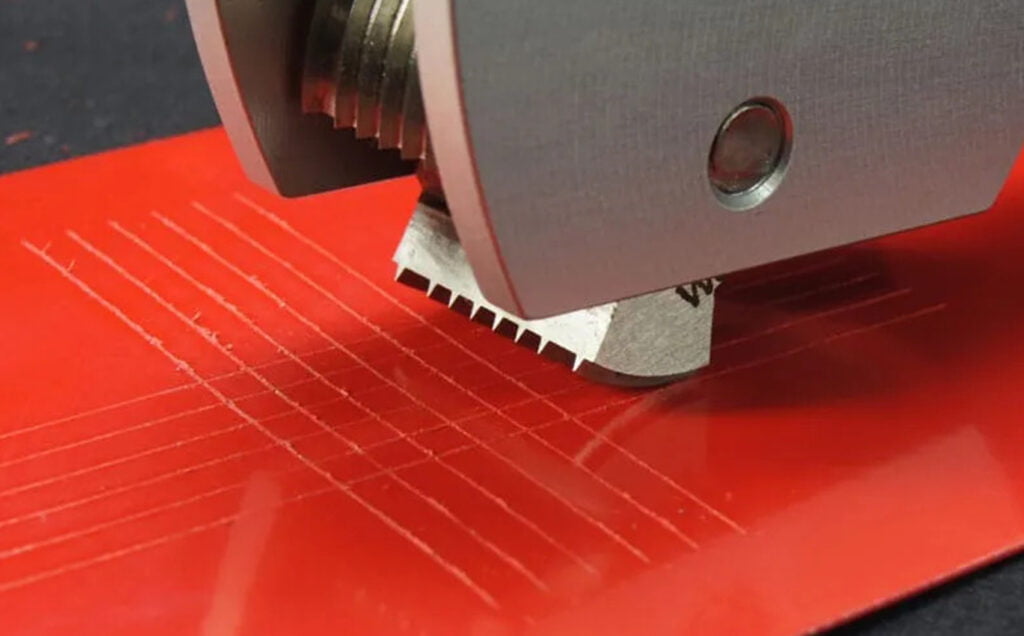
Scratch testing is a technique used to evaluate the hardness and durability of a material. It involves using a pointed or sharp tool to make a scratch on the surface of the material and then observing the extent of the damage caused by the scratch. The scratch can be made using various tools, such as a diamond-tipped stylus or a tungsten carbide needle, depending on the specific application.
In retail displays, where the majority of product finishes are painted or printed with ink, scratch testing is an effective way of checking the adhesion of pigmented inks, with the Hundred Gram Test being a standard scratch test method.
The test consists of making a series of small cuts or incisions in the coating at regular intervals to form a cross-shaped pattern on the surface. A piece of tape is then applied to the crosshatch pattern and pressed down firmly. The tape is then pulled away at an angle of 90 degrees to the surface and quickly torn off. The amount of coating that comes off with the tape is assessed according to a standardized rating scale.
There are also a number of steps that must be done before a retail display can leave the factory.
1. assembled products. Custom retail display furniture if not assembled before leaving the factory has a high probability will happen products that have been shipped to the mall to take can not be installed embarrassing things.
2. Test the power transformer. With light or display displays have become very common, power to the power supply will make the light source not bright enough or directly to the electronics to destroy. In the factory before the product for the power supply test is very important.